Current Research Projects
Current scientific interest is primarily related to nanotechnology, high energy density materials, and novel alternative energy sources.
The following fundamental topics are currently under investigation:
Solid Flame
Throughout history, people have tried to understand what skills and abilities qualitatively set the man apart from other living beings. Thinkers have come up with many definitions, including the ability to use tools, linguistic communication, social organization of society, the wearing of clothing. But, if you look closely at the lives of our smaller brothers, people have found all of these capabilities, even for animals. Indeed, many animals use tools (with a stick to get a fruit, stone - to break a nut ...), there is a kind of language in the majority of animals, and even the dolphins call each other by personal names; social organization of an anthill, a beehive or a wolf pack has stood test millions of years which cannot be said of human civilization. Clothes are not worn by all human tribes (what about young children and nudists?), but some shellfish and octopus cleverly "dress up" in the foreign shell.
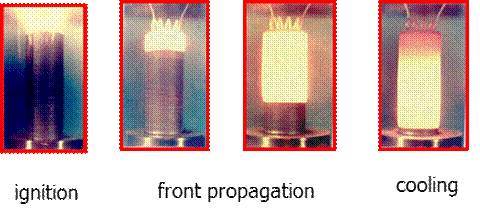
And yet there is the ability that no one on Earth, except the man, possesses. It is the skill to make fire and use it. The exclusivity of this skills was well understood by our ancestors, indeed, the myths and legends of many peoples' ownership of fire makes people rivals of the gods. The ancient Greek philosopher Protagoras argued that man exists only thanks to the fire donated by Promethean, the wisdom bestowed by Athena (i.e. intellect), and the general device provided by Zeus. In such a sequence of importance: the fire - intellect - society.. It seems to be that all kinds of combustion have long been discovered and made to serve the people. However, in the late sixties of the last century, a group of Russian scientists has discovered a new class of combustion processes, which they called solid flame. Based on this phenomenon a novel technology for synthesis of advanced materials, so-called Self-propagating High-temperature Synthesis (SHS) has been developed (see details in presentationpdf).
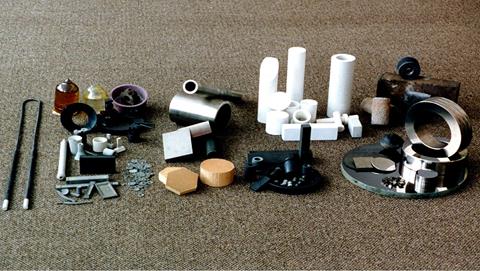
Relevant Publications: Adv. Chem. Eng., 1998, 24,79-226; Curr. Opin. Sol. State Mat. Sci.12, 2008, 44–50; J. Prog. Ener. Comb. Sci., 34(3) 377-416 (2008); Comb., Expl. Shock Waves, 4 (3), 243-266 (2010).
Nanomaterails by Solution Combustion Synthesis
Solution combustion synthesis (SCS) is a versatile, simple and rapid process, which allows effective synthesis of a variety of nanomaterials. This process involves a self-sustained reaction in homogeneous solution of different oxidizers (e.g., metal nitrates) and fuels (e.g., urea, glycine, hydrazine). Depending on the type of the precursors, as well as on conditions used for the process organization, the SCS may occur as either volume or layer-by-layer propagating combustion modes. The former mode involves reaction in a homogeneous aqueous oxidizer– fuel solution that is uniformly heated by a constant temperature heating source (oven, hot plate, microwave etc.). In the latter case, the gel reactive media is ignited locally at one point resulting in a combustion wave that propagates in a self-sustained way along the reaction media
![]() |
nickel nitrate + glycine gel |
here are many publications on using the solution combustion as a method of synthesis of a various nanopowders. The nano-scale size of combustion products and their high specific surface are caused by several reasons: (i) molecular level of mixing of reagents in the solution, which ensures an extremely small scale of heterogeneity of the initial sol-gels; (ii) large amount of gas-phase products whose intense liberation prevents agglomeration (sintering) of solid-phase products; (iii) specific features of formation of the solid-phase product in the form of thin layers or suspensions, which is responsible for the high rate of product cooling, i.e., short duration (<1 sec) of the high-temperature zone behind the combustion wave.
Recent
breakthrough in the field:
Synthesis of pure metals (Ni,Cu,Fe) and alloys (Ni-Cu-Fe);
Establishing of intrinsic reaction mechanisms in reactive gels;
Development of new modifications of SCS,i.e. impregnated layer SCS and template SCS
(see more details in presentation)pdf
Recent Relevant Publications: Proc. Comb. Ins, 31(2), 1789-1795 (2007); Curr. Opin. Sol. State Mat. Sci.12, 2008, 44–50; AIChE J., 57(8), 2207-2214 (2011); AIChE J., 57(12) 3473- 3479 (2011); App. Catal. A: General, 401(1-2), 20-28 (2011).
Reactive Multilayer Nanofoils
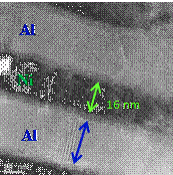
Reactive
multilayer foils (RMLFs), which are
composed of altering nano-scale layers of solid reactants, represent a class of
functional nano-materials with numerous applications. The nano-RMLF is usually
produced by means of sequential magnetron deposition of many (up to thousands of)
non-mixing layers of different metals or non-metals (e.g., Ni/Al, Pt/Al, and
Nb/Si) with the thickness of each layer ranging from several to hundreds of
nanometers. When short-term heat impulse (by electric spark, hot filament,
laser beam, etc.) is locally applied to the nano-RMLF, a heterogeneous exothermic
reaction between reactant layers starts in this area and the generated heat
spreads into the non-reacted adjacent region, consequently initiating reaction
there.
Thus due to the inner heat from the interaction of initial elements and
the formation of appropriate compounds (e.g., NiAl, PtAl, and NbSi), the
self-sustained wave of exothermic reaction with temperatures up to 3000K
propagates throughout the whole RMLF sample. This phenomenon is akin to
processes such as self-propagating high temperature synthesis and explosive
crystallization; however, it possesses many specific features which have yet to be
studied. An intriguing characteristic of this process is the extremely high
velocity of the reaction wave propagation, for example 10m/s (Ni/Al) or 90 m/s
(Pt/Al). To know why please see presentationpdf.
Recent Relevant Publications:Appl. Phys. Let., 101(6) Article Number: 063119,
(2012); Surf. Coat. Tech., 215, 485-492 (2013).
Reactive Nano-Composites
High energy ball milling (HEBM), when applied
to reactive heterogeneous systems, is a powerful tool to control the media microstructure
and thus leads to different applications. First, HEBM allows rapid combustion synthesis
of materials in the low exothermic systems, which in conventional state cannot
sustain self-propagating reaction regime. Second, such mechanical treatment typically
results in formation of composite reactive particles which
permits designing the microstructure and hence properties of materials (e.g. to
produce the Functionally Graded Materials).
Third, HEMB is a unique approach
for synthesis of nano-materials. Finally, tuning the sensitivity of the
reactive systems by HEBM leads to various special applications related to rapid
ignition, gasless high temperature preheating, etc. In the above context, the
fundamental knowledge of the phenomena which take place during HEBM of reactive
powder mixtures is critic al to design
different technologies (see presentationspdf and posterpdf.
Recent Relevant Publications: J. Phys. Chem., A, 113, 13541–13547 (2009); Phys. B-Cond. Matter., 405, 778–784 (2010); J. Appl. Phys. 113 (2), 024302-024302-10 (2013).
Reactive Joining of Refractory and Dissimilar Materials
With the increased demand for more mobile combat forces, there is a need for lighter armor materials that can withstand light to medium warfare threats and still be economical. Consequently, the development of composites with tailored properties is drawing greater attention. Among them layered composites that consist of joined ceramic-metal parts, e.g. a hard ceramic front face and a soft metal back face are of special interest. However , when two such dissimilar materials with large differences in their structural and physical properties are bonded, a considerable change in the normal and high transverse shear stresses typically occur at the interface during fabrication and operation. This phenomenon often leads to delamination of materials at the ceramic/metal interface and poor load-bearing performance. Thus, formation of a transitional interface between dissimilar materials during the joining process, where the composition and the microstructure are compatible with those of the components to be joined, can provide a solution to this problem. Also joining refractory materials, e.g. carbon-carbon composite with melting point above 4000 K is demanding. The well-known application is refurbishing of C-C composite brakes for automotive and aerospace applications. A considerable number of techniques have been developed in the past few decades for the joining of dissimilar and refractory materials, including laser welding,fusion bonding,explosive welding,combustion joining (CJ). The later approach is based on the so-called combustion synthesis method, which was initially developed for the synthesis of advanced materials,but now is attracting attention as a tool for joining various substances, and is discussed in detail in a recent review. This method relies on use of extremely exothermic gasless reactive mixtures, which are initially located in between pieces to be joined, for their “chemical” bonding (see scheme below and presentationspdf)
![]() |
![]() |
Recent Relevant Publications: Int. J. of SHS, 16 (1), 23-35 (2007); Rev. Sci. Inst., 78, 1 (2007); J. Mat. Res., 23 (1) 160-169 (2008); J. Eur. Ceram. Soc., 32 (14), 3809-3818 (2012)
Mechanical Stimulation of Energy Dense Materials
The high volumetric energy density of gasless reactive systems, like Ni/Al, compared to other reactive systems, such as TNT (7.14 kJcm_3>6.22 kJcm_3) [1, 2], makes them enticing for many practical applications. However, gasless reactive systems with micrometer-scale periodicity normally have reaction wave propagation rates that are extremely slow (typically 1–10 cm/s, which limit their ability to release energy rapidly. Recently, other heterogeneous reactive systems, the so-named super-thermites utilizing nanometric powders, were investigated. Loose powders of these materials exhibited propagation rates on the order of km/s, comparable to some detonating explosives. The basis for such an enhanced reaction propagation rate has been attributed to convective burning, which allows forward transfer of heat and mass through gaseous mechanisms rather than through slower, condensed phase pathways. High-energy ball milling (HEBM) has also been shown to have a significant effect on the thermal sensitivity of gasless systems. HEBM creates composite particles with a highly irregular, lamellar internal structure. Sensitivity in the system is increased through dramatic increases in interfacial area between reactants in the composite particles. Initiation of the reaction through methods other than direct heating has also been found to induce higher reaction propagation rates. Mechanically loading a material to induce chemical changes by application of a strong shock wave has been studied since the middle of the last century. The chemical processes occur as either shock-assisted reactions, where the shock wave modifies the material to allow the resulting thermal equilibration of the material to initiate reaction, or as shock-induced reactions, where the reaction occurs during the mechanical equilibration of the material. The ability of reactions to occur rapidly under the combined effects of strong compression and shear is another concept that is historically known, having been investigated for nearly a century. The consolidation of ceramic forming powders in explosively collapsed cylinder experiments has shown that reactions can initiate within shear localizations (shear bands). These reactions can either be limited to the materials within the shear band or can become self-propagating and consume the entirety of the sample. The objective of the current research is to compare the behavior of high-energy density systems with varying microstructures under both thermal and high-rate mechanical energy loadings. In particular, attention was given to the initiation of a high-rate reaction wave that travels near the impact velocity in normally low-rate gasless systems (see posterpdf).
![]() |
The high-speed reaction regime in nNi/nAl system is shown in this image sequence. This reaction was initiated at an impact velocity of 1070 m/s. Contrast is enhanced in images A and B. Plunger enters frame from right and its approximate position of plunger is outlined in framed B-H. Inter frame time is 7.25ms. |
Recent Relevant Publications; J. Phys. Chem. C,, 114, 35 14772-14780 (2010);J. Phys. Chem. C., 116 (39), 21027-21038 (2012); Propell. Explos. Pyrotech. 38 (3), (2013).